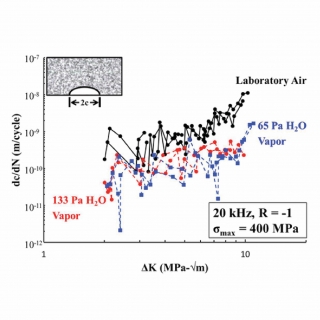
Environmental and Elevated Temperature Effects on Fatigue Loading of Titanium Alloys
Understanding the fatigue behavior of Titanium alloys is critical in order to accurately assess and design for their extensive use in aerospace applications, including turbine engine fan and compressor disks. Past and current research includes the investigation of environmental effects on the very high cycle fatigue behavior (N>108) of the widely used jet engine titanium alloy Ti6242, and into the roles of temperature and microstructure on its localized damage accumulation during dwell fatigue loading.
Dwell fatigue is characterized by cyclic loading, where the load is held constant for a set period of time at the top of each loading peak to create a trapezoidal waveform. This hold at peak stress is used to model the constant high mean stress that the component experiences during cruising, between the plane’s take-off and landing. These flight cycles dramatically reduce the lifetime of fan and compressor disks compared to lifetime estimates based on purely cyclic fatigue loading. Although near alpha titanium alloys have a large dwell sensitivity, mainly owing to the phenomenon of load shedding in the alpha grains, the mechanistic hypotheses for this behavior have not been rigorously tested. Dwell sensitivity and load shedding depend on the local microstructure, specifically microtextured regions (MTRs) and their intensity (microtexture refers to the clustering of similarly oriented α grains or particles, and the intensity is a function of the size, area fraction, and angular spread of the MTR; this microtexture is known to assist in the formation of fatigue cracks on both the local and global scale). Elevated temperature, dwell fatigue experiments across length scales are underway in combination with the statistical assessment of the effects of temperature and MTR zone characteristics on the initiation and propagation of localized damage in these alloys. This information will be used to develop constitutive relationships for use in improved fatigue models to more precisely track the evolution of stresses and defects at a both a local and global level, resulting in advances that will be directly utilized in both the military and commercial aerospace markets towards a safer and less costly fleet.